Decrypt roundness: definition and meaning
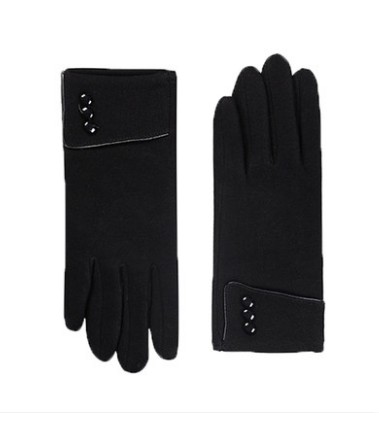
In engineering and manufacturing, "roundness" is a key geometric parameter, which determines whether a circular part really presents an ideal circular profile. Accurate roundness is not only the pursuit of aesthetics, but also has a profound impact on the function and service life of the product. For example, in the design of automobile engine blocks, if the ideal state cannot be achieved, it may lead to problems such as low operating efficiency, increased friction and even frequent failures. Therefore, for high-performance mechanical equipment, ensuring that each rotating element has a very high degree of roundness is an essential part.
In fact, many high-tech industries rely on extremely high-precision cylindrical parts to support their operations. From aerospace to medical equipment, to everyday items such as watch gears, all of which rely on precise circular motion to maximize effectiveness. Because of this, scientists are constantly committed to the development of new technologies and methods in order to obtain a more perfect roundness.
Methodology for measuring roundness
To accurately measure the roundness of an object, engineers use a variety of tools and techniques. Early people mainly used manual or semi-automatic calipers to make preliminary estimates, but this method has many limitations-it is difficult to capture subtle errors and takes a long time. With advances in technology, modern equipment such as high-resolution image analysis systems or 3D coordinate measuring machines (CMMs) can now be used for fast and detailed assessments.
In addition, non-contact detection devices designed based on optical principles are also becoming increasingly popular. The most typical one is the laser scanner, which can construct the complete morphological information of the surface to be measured by emitting a continuous beam and receiving the reflected signal. This not only greatly improves work efficiency, but also ensures that the results are true and reliable. Of course, in the specific implementation process also need to follow the provisions of ISO and related international standards, in order to achieve a unified standard of high-quality evaluation.
Challenge and Innovation: Breaking the Traditional Limits
Since the industrial revolution, efforts to improve roundness processing technology have never stopped. In particular, the lathe, as a basic metal cutting machine tool, has undergone many major innovations in the past two hundred years. The earliest steam power drive has gradually evolved into the wide application of electric motors and even numerical control systems, and every progress is accompanied by higher precision requirements. After entering the new century, ultra-precision grinding technology and nano-scale surface treatment process gradually emerged, paving the way for achieving an unprecedented level of roundness.
The latest research shows that by introducing advanced material synthesis technology and optimizing heat treatment conditions, the deformation tolerance can be effectively reduced and the crystal structure distribution can be controlled at the micro level. This means that even special components working in extreme environments can maintain long-term stable performance. Despite all the difficulties, researchers continue to move forward with confidence and look forward to more breakthroughs.
Application case study: the secret of success lies in the details
Let's focus on some real-world scenarios! Here are some typical cases worth sharing. The first is the success story from the aerospace industry, which is known for its strict standards. Behind each mission is the result of countless days and nights of R & D accumulation and technical research. In this process, enterprises fully realize the importance of mastering the core technology, and have the courage to try new materials and process routes. In the end, we won the trust and support of our customers with our rigorous attitude and perfect service.
Another example is the transformation of the medical device industry. In the face of fierce market competition pressure, a local brand resolutely invested heavily to establish its own R & D center, focusing on overcoming the bottleneck problem that has been plagued for a long time. After unremitting efforts, they finally found a suitable model for their own development, and quickly grew into the industry leader. This shows that as long as you carve every link with your heart, you can reap unexpected results.
A New Era of Quality Assurance: Automation and Intelligence
Today's era of intelligent manufacturing marks a new starting point. The integrated platform formed by the combination of automated fixtures and intelligent sensor networks is changing the entire production process management landscape. This system can track the state change of each processing step in the whole process, and immediately start the alarm mechanism to remind the operator to pay attention to the inspection and correction once the abnormality is found. At the same time, with the decision support provided by the big data analysis engine, managers can mine potential laws from the massive historical records to guide the planning and deployment of similar projects in the future.
It is worth mentioning that machine learning algorithms have shown broad application prospects on this basis. Through the learning and training model of past failure samples, we can foresee the possible risk points to a certain extent, and then take corresponding measures to prevent and resolve the crisis. In short, this concept of integration of cutting-edge information technology will lead the future direction of development.
Environmental protection and energy saving: the pursuit of excellence while not forgetting social responsibility
In the process of pursuing higher roundness, we must not forget our social responsibilities. More and more enterprises begin to pay attention to the application and promotion of green environmental protection production process, aiming to minimize the occurrence of environmental pollution and resource waste. For example, the use of solar photovoltaic panels to supply power to drive machine tools not only saves electricity costs but also realizes the effective recycling of clean energy. In addition, the successful implementation of the recycling plan for waste materials has further consolidated the circular economy chain.
According to statistics, such measures not only help reduce overall operating costs by about 20%, but also create a positive brand image for the company and win public recognition and praise
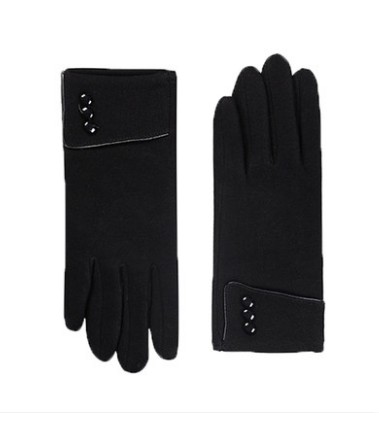